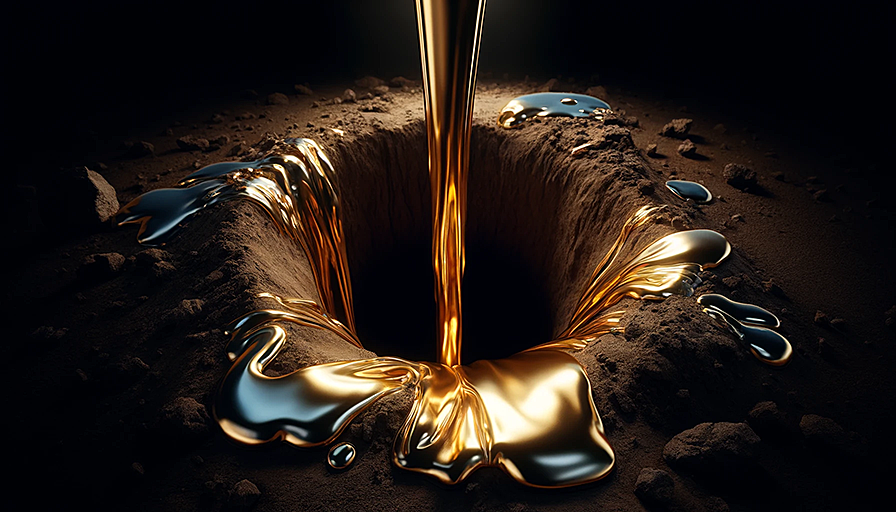
Why Thermal Conductivity Tests Can Wait
by GeoFease | Sept. 26, 2024, 8:21 p.m.
When planning a ground source heat pump (GSHP) system for a building project, the standard recommendation often includes spending $30,000 to $50,000 on drilling a test borehole and conducting thermal conductivity tests. However, this investment can be premature and costly without first assessing several critical factors:
- Optimal borehole location
- Appropriate borehole depth
- Suitable U-tube dimensions
Before any drilling begins, it is essential to develop a preliminary ground heat exchanger (GHX) model based on hourly energy simulations and site-specific geological data. The GHX configuration—including the number and depth of boreholes—should align with site constraints, while the required heat pump capacity dictates the necessary flow rate. These variables influence the pressure drop through the boreholes, which in turn determines the appropriate pipe sizing for efficient thermal exchange and minimal pumping energy.
Reviewing local water well or drilling logs and consulting with experienced drilling contractors or geologists familiar with the region’s subsurface conditions provides a preliminary assessment of site geology. This approach accurately estimates the average thermal conductivity and diffusivity of the soil and rock at the project site, eliminating the need for costly test boreholes.
This case study advocates for a comprehensive feasibility study as a more prudent investment during the initial project phase. Conducting a sensitivity analysis on a real-world example demonstrates how variations in energy loads and thermal properties impact GHX sizing, ultimately supporting the case for a more informed and cost-effective feasibility assessment.
Scenario 1: Building Load Excluding Domestic Hot Water
An energy model for a multi-family condominium in Ontario, Canada, showed a peak cooling demand of 175 tons, excluding domestic hot water (DHW) loads. Regional water well logs and discussions with local drillers estimated the site’s thermal conductivity (TC) at 1.4 Btu/hr·ft·°F and thermal diffusivity (TD) at 0.9 ft²/day. Based on these properties and energy demands, the simulations determine that the project requires a total borehole length of 36,120 feet. Heat pump manufacturers typically recommend a flow rate of about 3 gallons per minute (gpm) per ton, leading to a required flow rate of 525 gpm for the project.
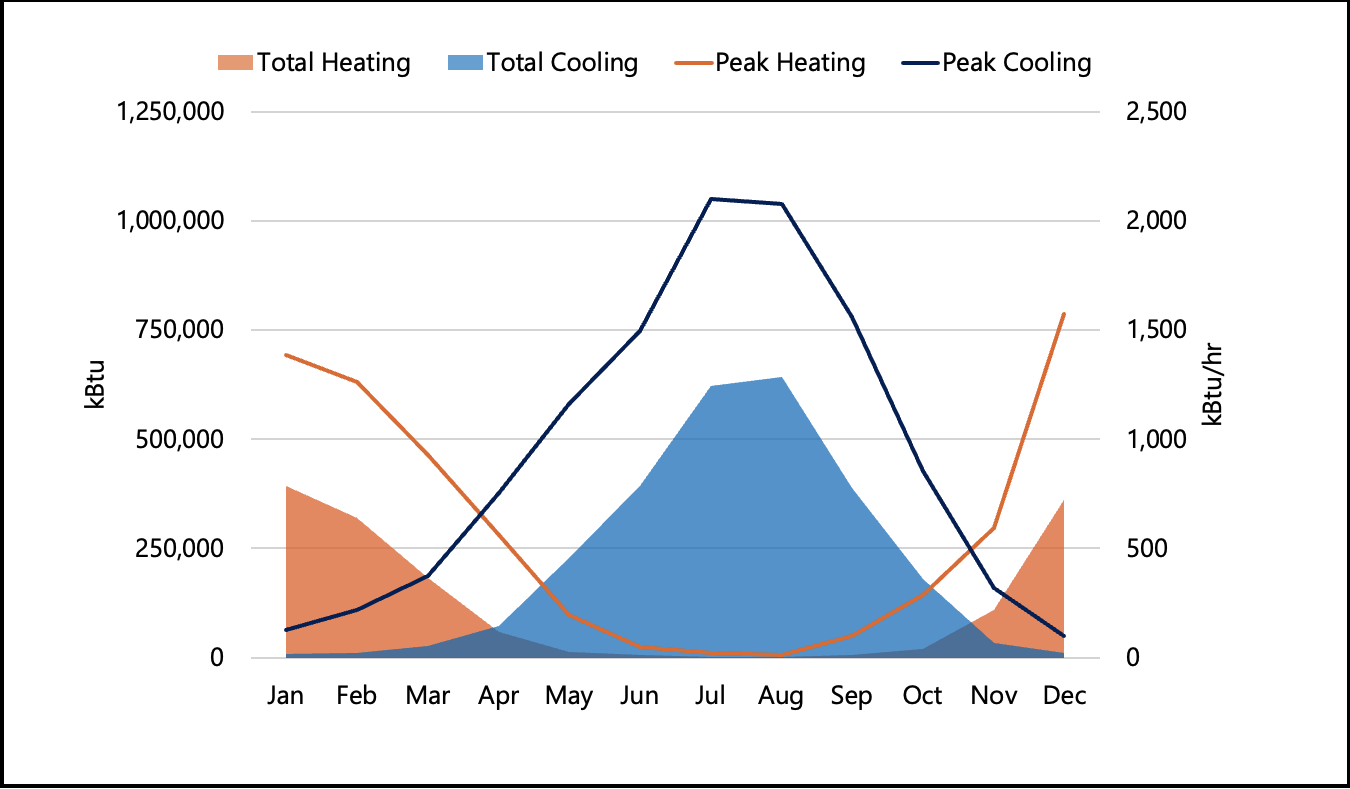
Building Energy Load Excluding DHW
The site has sufficient space to accommodate 60 boreholes, each spaced 20 feet apart. Drilling these boreholes to a depth of 600 feet achieves the required total borehole length of 36,120 feet. Dividing the total flow rate (525 gpm) among the 60 boreholes requires each borehole to handle just under 9 gpm during peak load conditions. Hydraulic modeling with a 20% propylene glycol heat exchange fluid shows a pressure drop of less than 30 feet of head throughout the GHX system, while maintaining a Reynolds number greater than 4,100—ensuring efficient flow and heat transfer.
In this scenario, the recommendation was to drill a test borehole to a depth of 600 feet using 1.25-inch SDR11 HDPE piping. The estimated drilling cost was $45 per foot, totaling $27,000. Adding the $8,000 cost for the thermal conductivity test brought the total estimated cost for the test borehole to $35,000.
A sensitivity analysis highlighted the impact of variations in thermal conductivity. Adjusting the initial TC estimate downward to 1.3 Btu/hr·ft·°F, while keeping TD constant at 0.9 ft²/day, would increase the required borehole length by 3,500 feet—a 9% rise. Conversely, a higher TC of 1.5 Btu/hr·ft·°F would reduce the total borehole length to 35,280 feet, a 3% decrease.
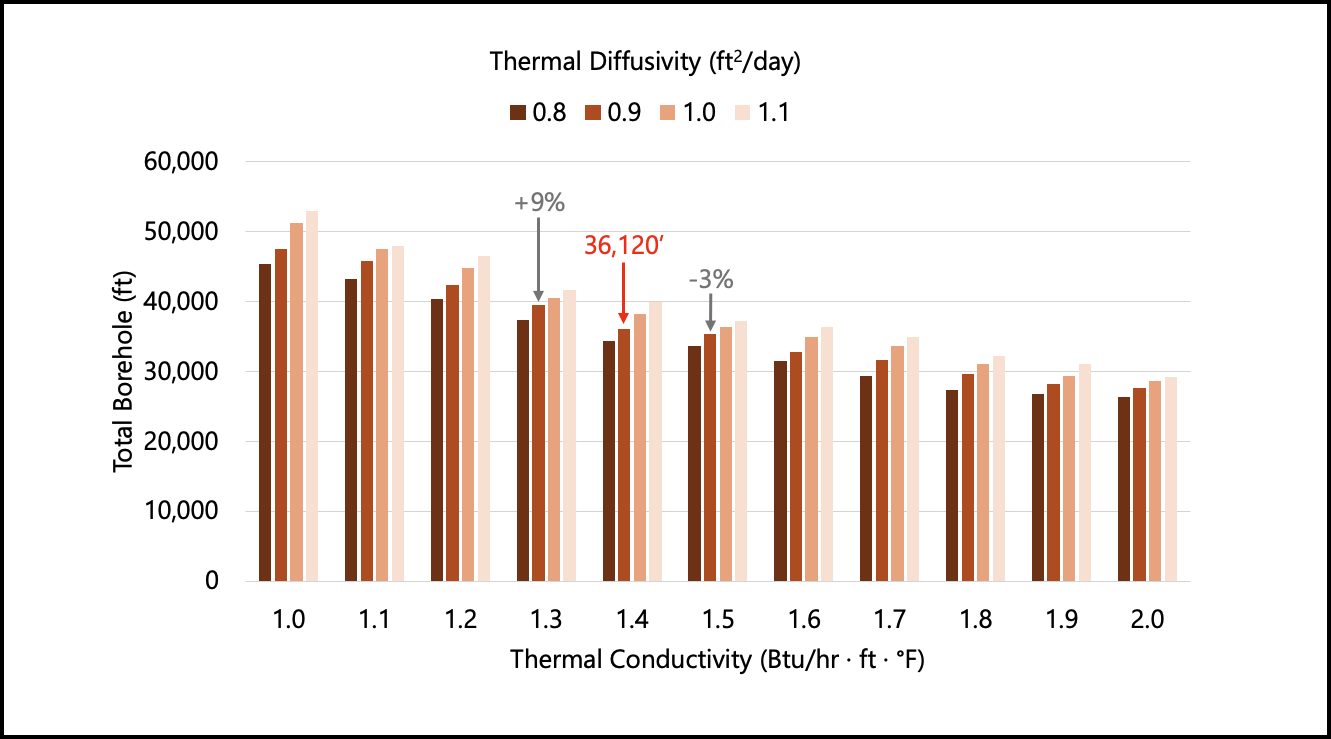
Impact of Thermal Conductivity and Diffusivity on Borehole Length Excluding DHW Loads
Scenario 2: Including Domestic Hot Water Loads
Incorporating domestic hot water (DHW) loads into the building model balanced the energy demand by increasing heat extraction from the GHX, reducing the total required borehole length from 36,120 feet to 29,700 feet—an 18% decrease. This reduction allows for more flexibility in borehole configuration. For example, the site can support 60 boreholes at 500 feet deep or 50 boreholes at 600 feet. Drilling contractors often recommend the 600-foot depth to minimize horizontal trenching and reduce the number of pipe connections, making this option more cost-effective.
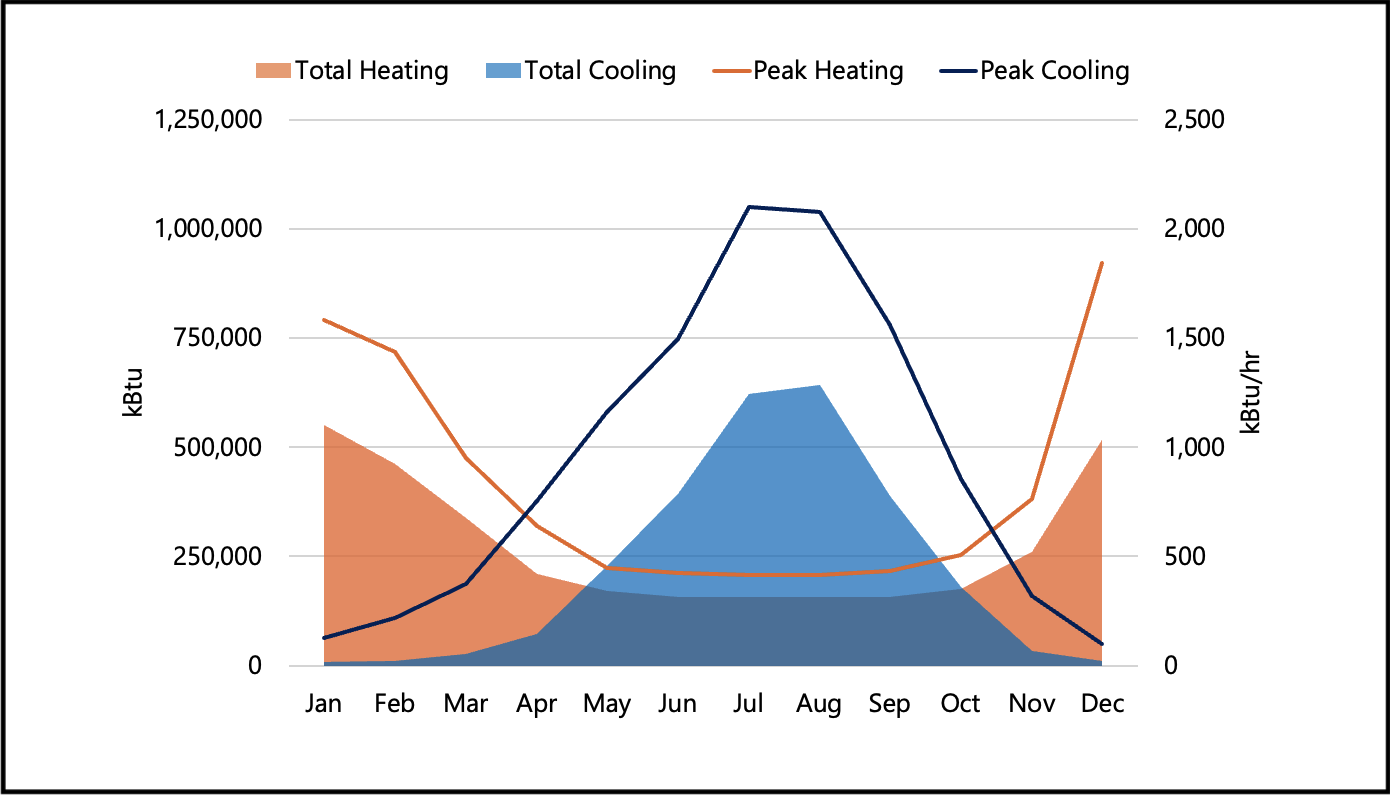
Building Energy Load Including DHW
Another option involves installing 48 boreholes at 620 feet deep, which provides better flexibility for the supply and return piping layout. Although the peak cooling load remains at 175 tons, requiring a total flow rate of 525 gpm, this configuration increases the flow rate through each borehole to approximately 11 gpm. In this setup, using 1.25-inch U-tubes would result in a pressure drop exceeding 40 feet of head. To address this issue, upgrading to 1.50-inch SDR11 piping would reduce the pressure drop to below 20 feet of head, significantly lowering future pumping energy requirements while maintaining Reynolds numbers above 5,600 with a 20% propylene glycol solution.
This configuration recommends drilling a test borehole to a depth of 620 feet with 1.50-inch SDR11 piping. Including DHW loads in the energy model shows that variations in thermal conductivity have a smaller impact on the required total borehole length. The surrounding soil functions more effectively as a heat storage medium, reducing the influence of conductivity on system performance.
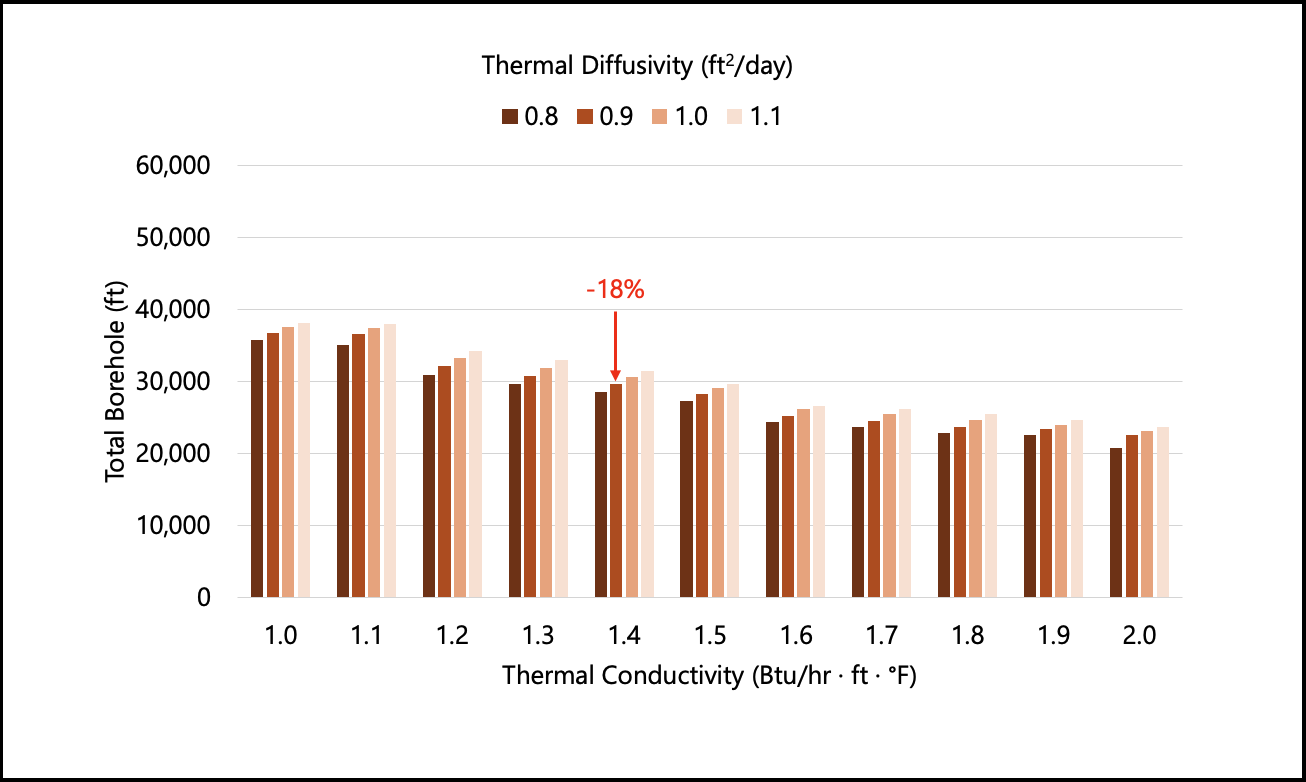
Impact of Thermal Conductivity and Diffusivity on Borehole Length Including DHW Loads
This case study illustrates that balancing energy loads, such as incorporating domestic hot water, significantly reduces the influence of soil thermal properties on GHX sizing. It also shows how thermal conductivity specifications can change during the feasibility stage. For example, Scenario 1 specifies a thermal conductivity test at a 600-foot depth using 1.25-inch SDR11 piping, while Scenario 2 recommends a 620-foot depth with 1.50-inch SDR11 piping.
Many in the GSHP industry mistakenly believe that drilling a test borehole should always be the first step. However, this can result in unnecessary costs without a clear understanding of the project’s specific requirements. A comprehensive feasibility study, costing around $10,000 to $50,000, offers valuable insights and refines the preliminary GHX design through various sensitivity analyses. After deciding to proceed with a geothermal system, conducting a TC test validates the assumptions from the feasibility study, ensuring a well-informed and cost-effective installation.